In the complex tapestry of contemporary business operations, the meticulous analysis of failures and the implementation of effective corrective actions are indispensable for achieving operational excellence. The Failure Reporting, Analysis and Corrective Action System (FRACAS) offers a systematic approach to identifying, analyzing, and preventing recurrence of problems. This blog post delves into the intricate world of FRACAS, highlighting its significance and outlining the robust methodology it provides to organizations keen on optimizing their processes and products. Through this exploration, readers will gain a comprehensive understanding of how FRACAS can become an integral part of their business practices and substantially contribute to their success.
Understanding FRACAS
Definition and explanation of Failure Reporting
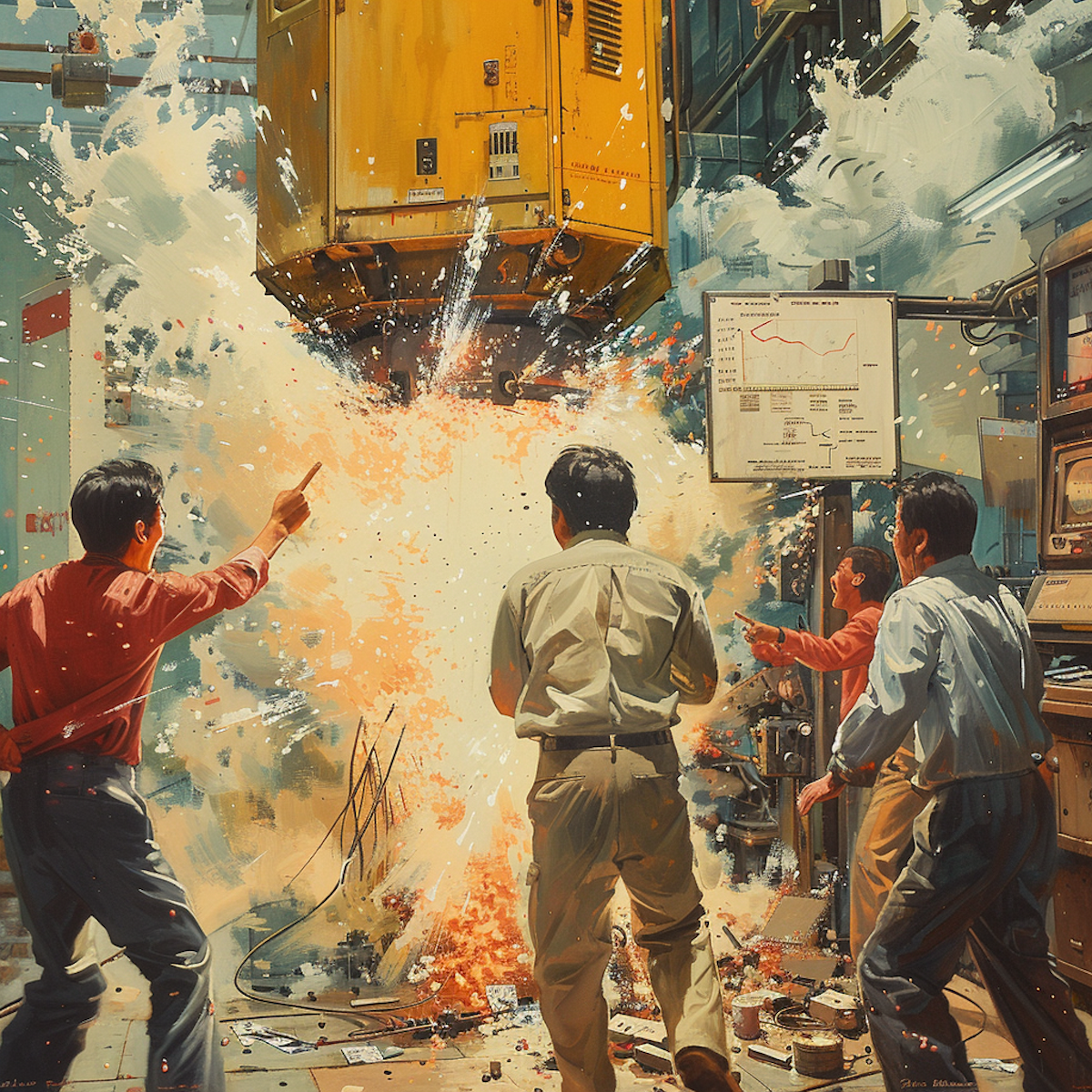
In the realm of operational management, failure reporting serves as the cornerstone for any systematic improvement process. It is the initial step in the FRACAS methodology, documenting details of a failure occurrence with precision. Problem solving course curricula often emphasize the necessity for professionals to understand the instances in which this reporting is vital. For example, when an assembly line experiences unexpected downtime or a software system crashes, these incidents need to be meticulously recorded.
The benefits of accurate and timely failure reporting are multifold. Companies that excel in this practice are able to reduce downtime, streamline repair processes, and enhance product reliability. Furthermore, consistent failure reporting fosters a culture of transparency and continuous improvement. This culture enables employees at all levels to contribute to the problem-solving process, ensuring that potential issues are identified and addressed before they escalate.
Detailed look at Analysis in FRACAS
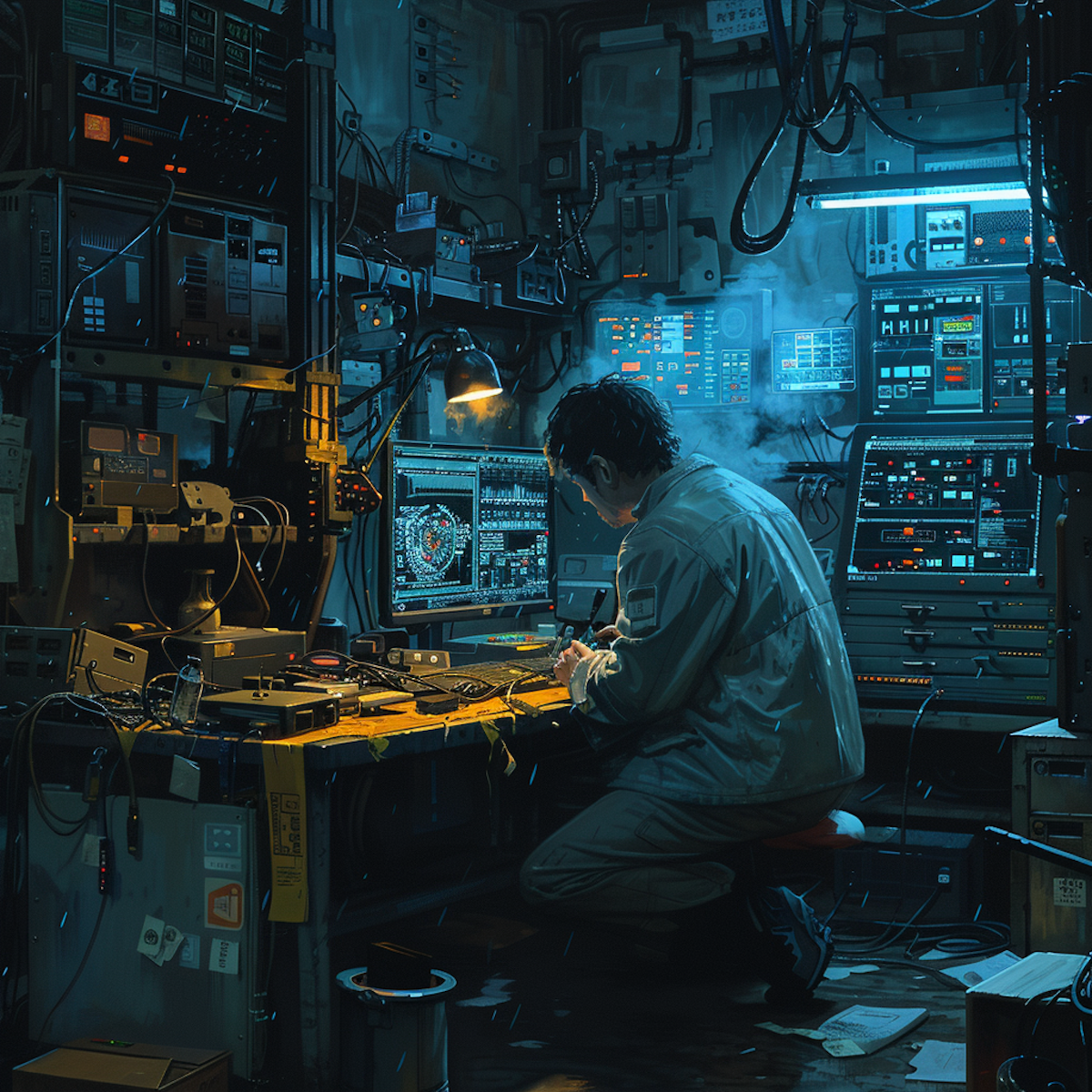
Once a failure is reported, analysis is the subsequent step that plays a pivotal role in identifying the root causes of the recorded incidents. This process employs varying analysis approaches and techniques, from simple 'Five Whys' questioning to complex statistical methods. For instance, the use of fault tree analysis or failure mode and effects analysis (FMEA) can reveal hidden connections between various operational aspects and the recorded failure.
The diversity of analysis techniques ensures that FRACAS can be adapted to address the specificities of different types of failures, whether mechanical, electrical, or human-driven. It scrutinizes data to understand the conditions under which a failure occurred, paving the way for actionable insights. This in-depth, nuanced view is what allows FRACAS to move beyond superficial fixes and to focus on systemic solutions.
Examination of Corrective Action Systems
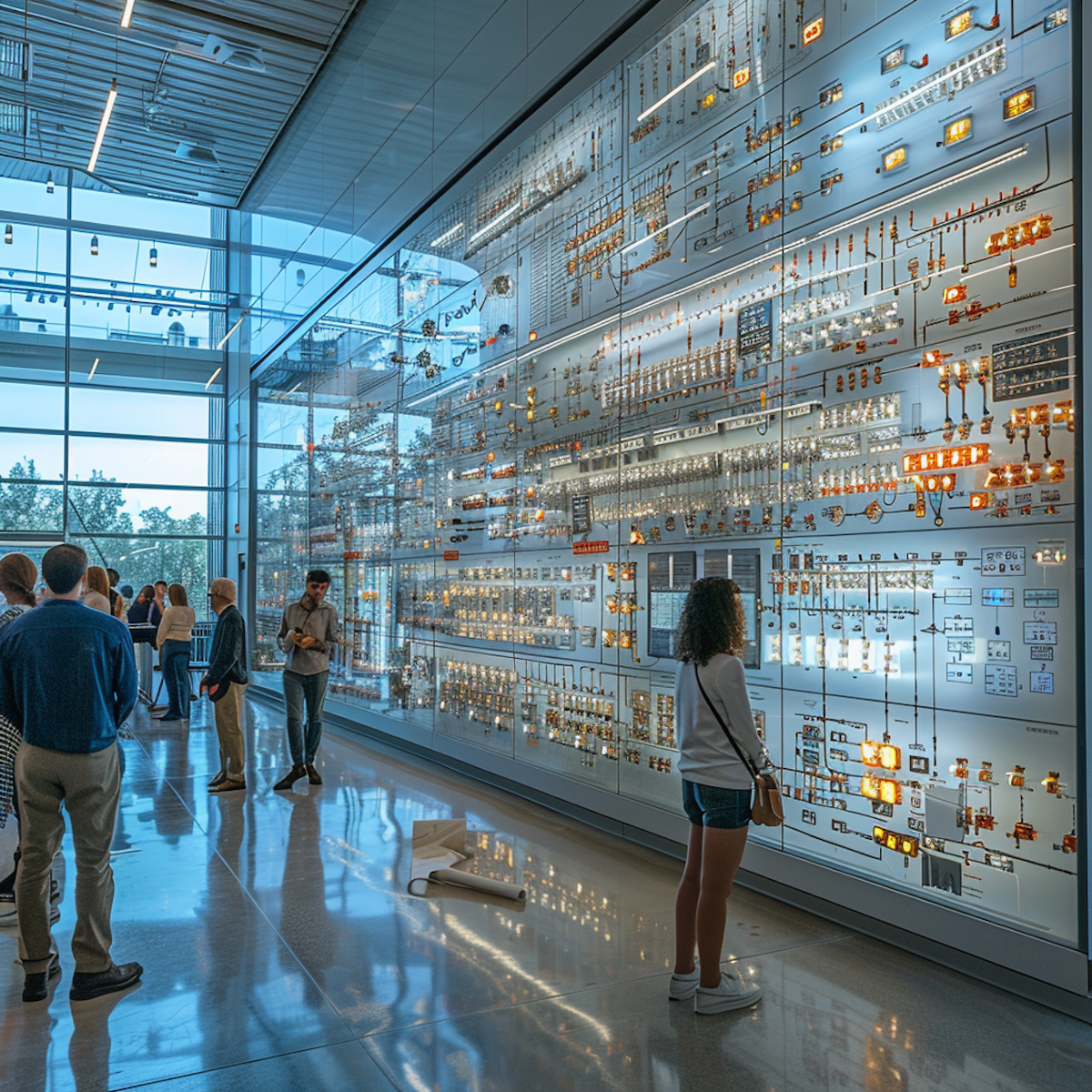
Implementing a well-structured Corrective Action System is imperative to the FRACAS process. Effective remediation entails a series of steps, starting from the determination of an appropriate corrective action, to its implementation, and through to monitoring its effectiveness. System-based correction rather than isolated fixes ensures that improvements are sustainable and integrated across the entire operation.
For instance, after a software malfunction is analyzed, corrective actions may involve not just code revisions but also enhancements to development protocols and testing procedures. Such holistic improvements address the immediate problem while reinforcing the overall resilience against similar future failures. This systematic approach fortifies the infrastructure against potential weaknesses and standardizes responses to operational hurdles.
Implementing FRACAS in Business Operations
Requirement analysis of FRACAS in different sectors
FRACAS is not a one-size-fits-all system; it requires customization to fit the unique demands of various sectors. A problem solving course designed for industry-specific challenges can provide the foundational knowledge necessary to adapt FRACAS effectively. For example, the aerospace industry prioritizes safety and would consequently have different FRACAS requirements than the consumer electronics sector, which might focus more on product longevity and customer satisfaction.
Real-world examples of successful FRACAS implementation abound, showcasing the system's versatility. In the pharmaceutical industry, FRACAS underpins quality control by tracing the genesis of any anomalies in drug production. Similarly, in the realm of information technology, FRACAS informs the maintenance strategies for data centers, ensuring high availability and minimizing service interruptions.
The process of incorporating FRACAS into existing workflow
To weave FRACAS seamlessly into an organization’s fabric, several considerations are key. The provision of proper training is essential, ensuring that staff members are well-versed in both the philosophy and practical application of the system. Online certificate programs tailored to FRACAS provide accessible training options for companies intent on upskilling their workforce.
Top management buy-in and support for a FRACAS initiative are equally vital. Without executive endorsement, the implementation might falter, lacking the necessary authority and resources. Executives must understand not only the potential return on investment but also the importance of fostering a culture that prioritizes continuous improvement and proactive problem management.
Potential challenges in implementing FRACAS and how to overcome them
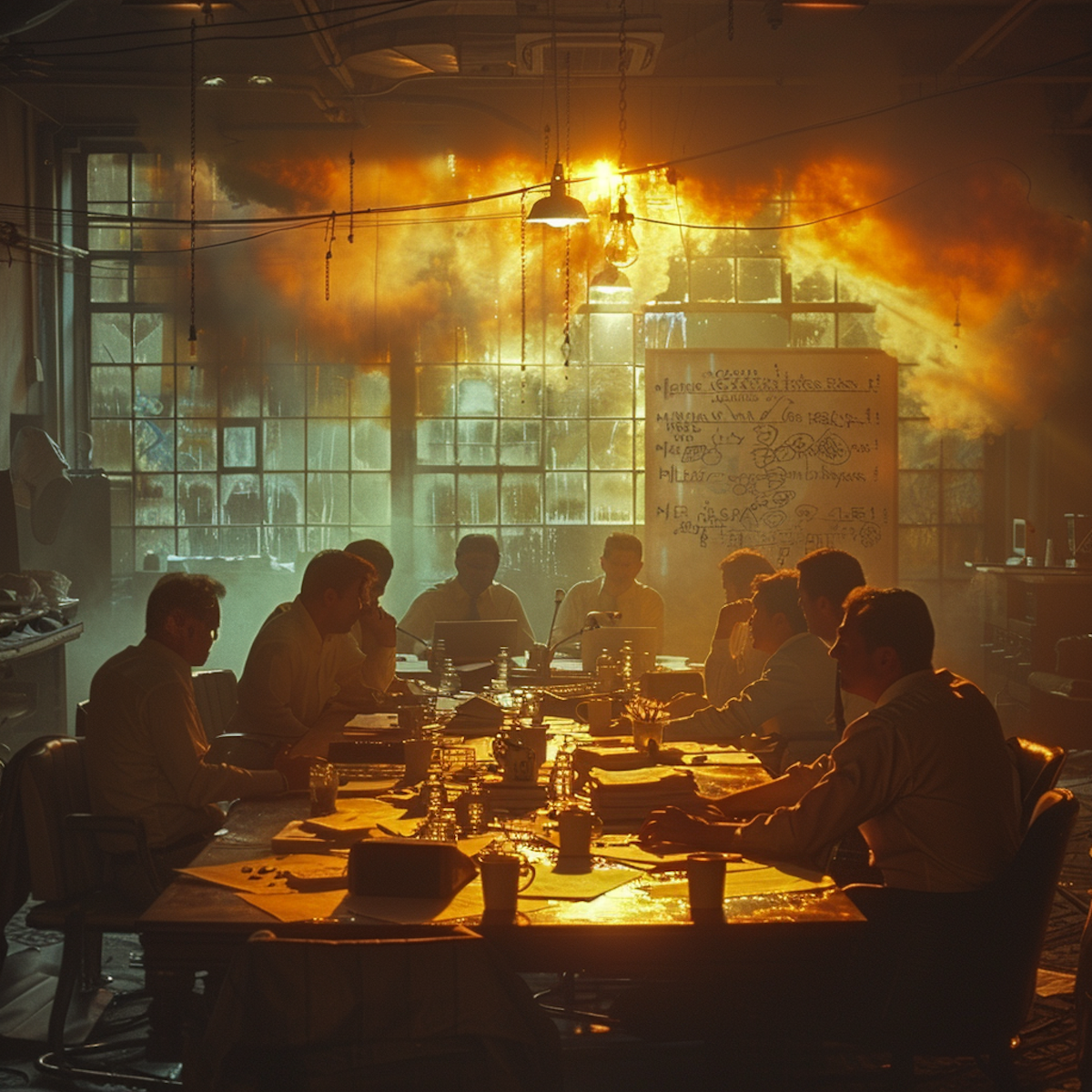
While FRACAS is robust, challenges in its implementation are not uncommon. Organizations frequently encounter hurdles such as resistance to change, data management complexities, and inadequate follow-up on corrective actions. Awareness of these pitfalls and a well-considered strategy to navigate them are crucial. For aspiration, one can review case studies where organizations have demonstrated effective FRACAS usage to streamline their processes and prevent the recurrence of errors.
Successful implementation often involves auditing current procedures, setting clear metrics for improvement, and ensuring there is a feedback mechanism to track the efficacy of corrective actions. Only through such sustained efforts and rigorous problem solving can an organization truly realize the potential of FRACAS.
Evaluating the Effectiveness of FRACAS
Key performance indicators and metrics for assessing FRACAS
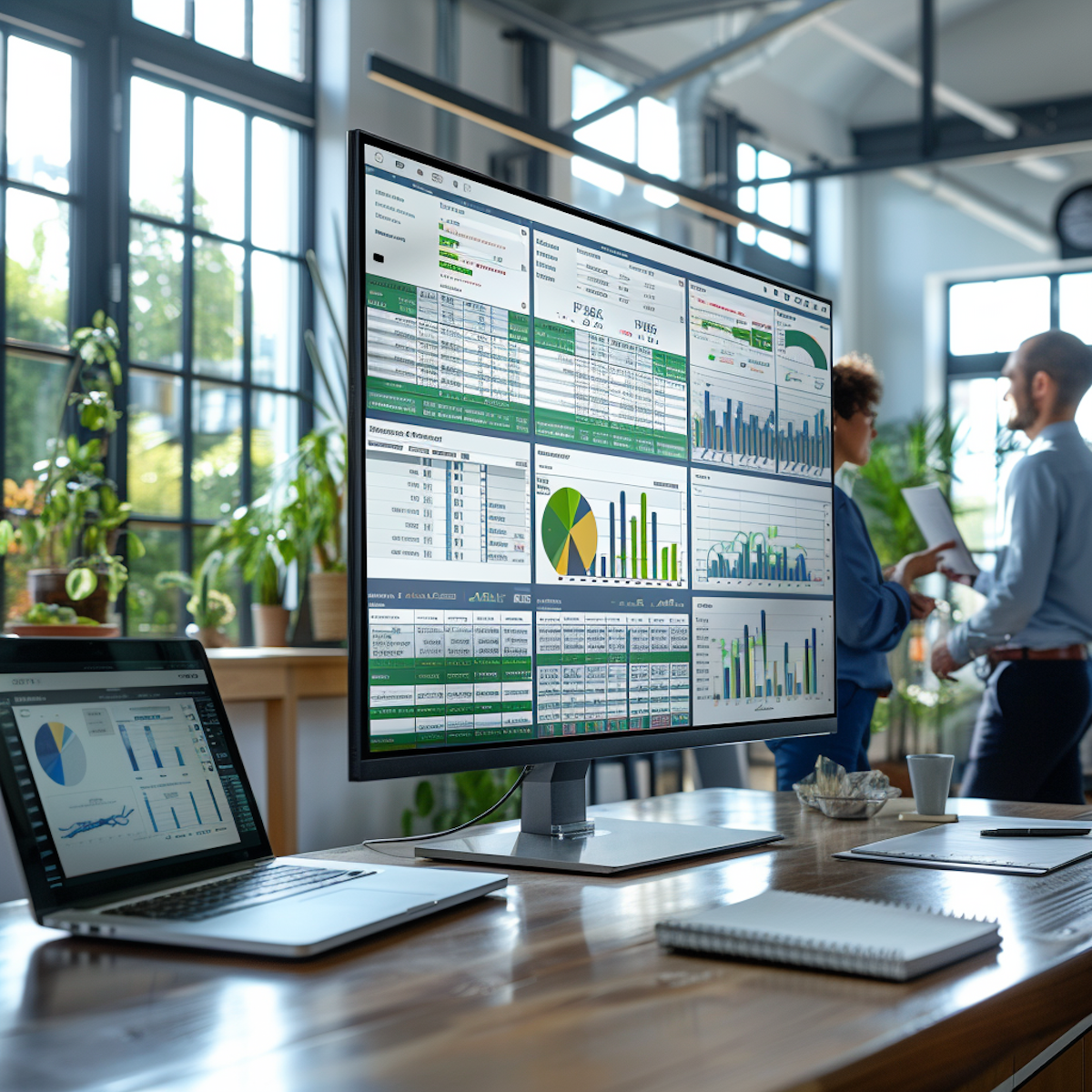
Measuring the success of FRACAS is intrinsic to its continued relevance and effectiveness within a business. Key performance indicators (KPIs) should be discerningly selected to align with the organization's overall objectives, such as reduction in failure rates, improvement in response times, and increased customer satisfaction rates. These metrics should reflect the thoroughness of the failure reporting, the depth of analysis conducted, and the durability of corrective actions implemented.
Continuous monitoring and evaluation serve as the guiding compass in assessing the FRACAS process. These activities not only track progress against set KPIs but also help identify new areas for improvement. It is a never-ending cycle of optimizing processes, where success is measured not as a finite point but as a trajectory of improvement.
Using feedback and data to improve FRACAS process
Data is the lifeblood of any FRACAS process and serves as the basis for decision making and system optimization. The importance of capturing accurate and comprehensive feedback cannot be overstated; it informs the iterative loop of adjusting and enhancing the FRACAS methodology. Real-life examples abound where feedback from cross-functional team evaluations has led to significant process refinements, reducing incident rates and bolstering operational robustness.
For example, after identifying a recurring failure in a production line, feedback from the shop floor staff led to procedural changes that decreased the incidence of the issue. Such tangible improvements act as a testament to the efficacy of a well-tuned FRACAS process.
The role of technology in enhancing FRACAS efficiency and effectiveness
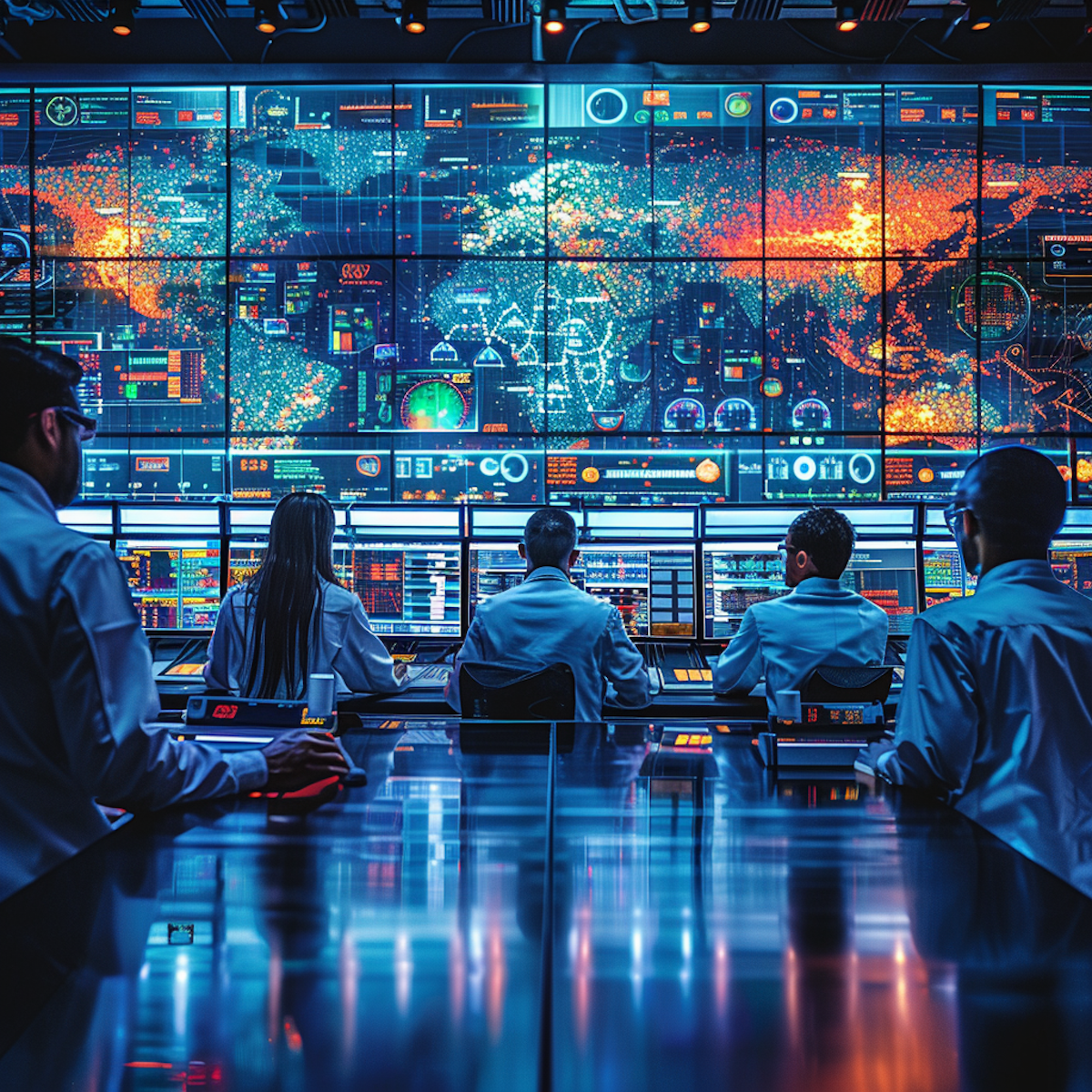
In our digital age, technology plays an ever-increasing role in enhancing the efficiency and effectiveness of FRACAS processes. Various FRACAS software solutions offer automation, real-time data analytics, and integrated reporting capabilities. This digitalization supersedes manual tracking and analysis, reducing human error and decreasing the time between failure detection and resolution.
A comparison of manual versus technology-driven FRACAS highlights numerous advantages, such as faster data retrieval, predictive analytics, and streamlined communication across departments. These technological innovations accelerate the feedback cycle, enabling swifter adaptation and continual optimization of both products and processes.
Conclusion
Throughout this discussion, the importance and multi-fold benefits of an effective FRACAS system in modern business operations have been clearly underscored. This comprehensive analysis should serve as both an enlightening read and an encouragement to organizations contemplating the integration of a structured, systematic approach to failure management in their operations.
As businesses grapple with the challenges of an increasingly competitive and complex environment, the implementation of FRACAS can be transformative, driving improvements in reliability, efficiency, and customer satisfaction. Hopefully, this post has sparked further interest and dialogue on the topic, inviting readers to explore the avenue of FRACAS with the same rigor and anticipation of success that the process itself embodies.