When I first stepped into the world of supply chain management, I had no idea how integral warehousing would become to my daily life. I vividly recall visiting a sprawling warehouse on the outskirts of my hometown—a massive building that seemed to breathe life into the products it housed. The hum of conveyor belts, the beeping of forklifts, and the meticulous organization of goods left an indelible impression on me. It became clear that warehousing wasn't just about storing products; it's about making strategic decisions that could optimize the entire supply chain management process.
Location
Size
Layout
Ownership
The Heartbeat of the Supply Chain: Warehousing
Warehousing is more than just a stopover point for goods; it's the heartbeat of the supply chain. A well-designed warehouse ensures that products flow smoothly from manufacturers to consumers, reducing delays and cutting costs. But achieving this efficiency isn't a matter of chance. It requires careful consideration of several critical factors:
1- Location
2- Size
3- Layout
4- Ownership
Let's delve into each of these areas, drawing from personal experiences, anecdotes, and industry best practices.
Location: Finding the Sweet Spot
Choosing the right location for a warehouse feels a bit like finding the perfect home. You want it to be in a neighborhood that's safe, accessible, and suits your needs. I remember when I was part of a team tasked with selecting a new warehouse location for a mid-sized retail company. We had to consider:
Proximity to Suppliers and Customers: Being close to suppliers reduces inbound shipping costs, while proximity to customers speeds up delivery times.
Digital Transformation İmpact On Supply Chain İnterview Question
Collaborative Logistics Strategies For Supply Chain Efficiency
Access to Transportation Networks: Highways, ports, and railroads are the arteries of logistics. A warehouse near these networks can reduce transit times and costs.
Labor Availability: A location with a skilled workforce ensures the warehouse operates smoothly.
Infrastructure and Utilities: Reliable power, water, and internet services are non-negotiable.
We mapped out various potential locations, weighing factors such as transportation costs and delivery times. In the end, we chose a site near a major highway intersection, which significantly reduced our transportation expenses and improved delivery speed. It was a decision that paid dividends in customer satisfaction and cost savings.
Size Matters: Scaling for Success
Determining the appropriate size for a warehouse is akin to planning for a family. You want enough space to accommodate growth but not so much that you're burdened with unnecessary costs.
When we expanded our operations, we faced the classic dilemma: How big should our new warehouse be? We considered:
1- Current Inventory Levels: Assessing the volume of stock-keeping units (SKUs) we handled.
2- Future Growth Projections: Estimating how our inventory might expand in the next 5-10 years.
3- Equipment and Machinery Needs: Allocating space for forklifts, conveyor systems, and other machinery.
Warehousing location and size define opportunity layout, optimize success and ownership, and enable long-term security.
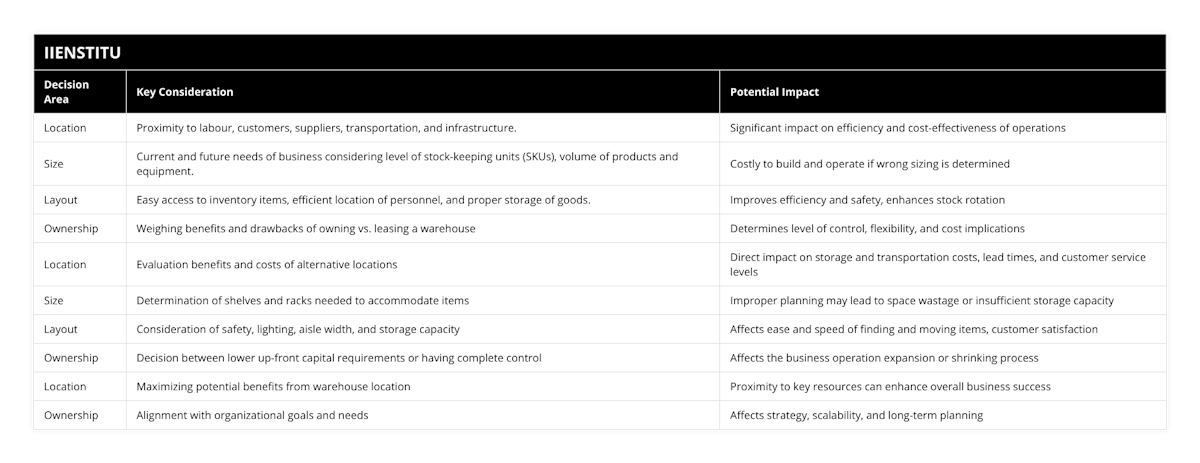
4- Operational Space: Including areas for loading docks, offices, and employee facilities.
We applied a formula from "Warehouse Management: A Complete Guide to Improving Efficiency and Minimizing Costs in the Modern Warehouse" by Gwynne Richards (2014), which helped us calculate our space requirements more accurately. By planning for the future, we avoided the pitfalls of outgrowing our space too quickly.
Italicized insight: It's better to have room to grow than to be cramped from the get-go.
Layout: Designing for Efficiency
A warehouse's layout is like the blueprint of a well-oiled machine. A thoughtful design can improve efficiency, safety, and employee satisfaction. During one project, we faced challenges with bottlenecks in the picking area, leading to delays.
To address this, we implemented the following steps:
Analyzed Workflow Patterns: Tracked how goods moved through the warehouse.
Redesigned Aisle Widths: Adjusted aisle sizes to allow for smoother traffic flow.
Optimized Storage Solutions: Utilized vertical space with higher shelving and installed pallet racking systems.
Implemented Technology: Introduced a warehouse management system (WMS) to coordinate activities.
After these changes, not only did our order fulfillment speed increase by 20%, but our workers also reported a better working environment.
*Bold statement: An efficient layout doesn't just boost productivity; it elevates the entire operation.*
Ownership: To Buy or to Lease?
Deciding whether to own or lease a warehouse is a significant financial decision. Early in my career, I worked with a startup that debated this very topic. The arguments centered around:
Benefits of Owning:
1- Asset Building: Ownership can be a long-term investment.
2- Control Over Customization: Ability to modify the facility to specific needs.
3- Stability: No worries about lease expirations or landlord issues.
Benefits of Leasing:
1- Lower Upfront Costs: Frees up capital for other investments.
2- Flexibility: Easier to relocate if business needs change.
3- Reduced Responsibility: Landlords typically handle major repairs and maintenance.
We ultimately chose to lease, which provided us the flexibility to adapt as the company grew. However, for more established businesses, ownership might offer the security and customization they require.
Underlined takeaway: Each option has its merits; the choice depends on the company's long-term strategy.
Optimizing the Supply Chain: Tips and Strategies
To optimize supply chain management processes, consider the following tips:
1- Conduct Regular Audits: Keep tabs on inventory levels and warehouse efficiency.
2- Invest in Technology: Utilize WMS and automation to streamline operations.
3- Train Staff Thoroughly: Well-trained employees are more efficient and make fewer errors.
4- Embrace Sustainability: Implement eco-friendly practices to reduce costs and appeal to environmentally conscious consumers.
By integrating these strategies, businesses can not only improve their warehousing operations but also enhance the overall supply chain performance.
Conclusion: The Foundation of Success
In the grand scheme of supply chain management, warehousing might seem like just one piece of the puzzle. However, as I've learned through years of experience, it's a foundational element that can make or break a company's efficiency and reputation.
By carefully considering the warehouse's location, sizing it appropriately, designing an efficient layout, and choosing the right ownership model, businesses can gain a competitive edge. These decisions require thoughtful analysis, but the rewards—reduced costs, improved customer satisfaction, and greater operational efficiency—are well worth the effort.
Final thought: Remember, every product that reaches a customer's hands has likely passed through a warehouse. Making that journey as smooth as possible starts with the decisions we make about these critical facilities.
References
Richards, G. (2014). Warehouse Management: A Complete Guide to Improving Efficiency and Minimizing Costs in the Modern Warehouse. Kogan Page Publishers.
Frazelle, E. (2002). World-Class Warehousing and Material Handling. McGraw-Hill.
Ackerman, K. B. (1997). Practical Handbook of Warehousing. Springer Science & Business Media.
Tompkins, J. A., & Smith, J. D. (1998). The Warehouse Management Handbook. Tompkins Press.