The pursuit of perfection in business processes is a relentless endeavor, marred by the human propensity to error. Yet, within such challenges reside opportunities—masterstrokes of ingenuity that promise not just to mitigate mistakes but to preemptively remove them from the equation altogether. One such masterstroke in the realm of continuous improvement and quality management is Poka-Yoke, a Japanese term that, when peeled back to its core, reveals the profound simplicity and effectiveness of mistake-proofing.
his article delves deep into the world of Poka-Yoke, unraveling its concepts, significance, and nuanced applications across industries, and underscores how this technique, fundamental to Lean thinking and Six Sigma, is indispensable for businesses aiming to rise above the ordinary.
Introduction to Poka-Yoke
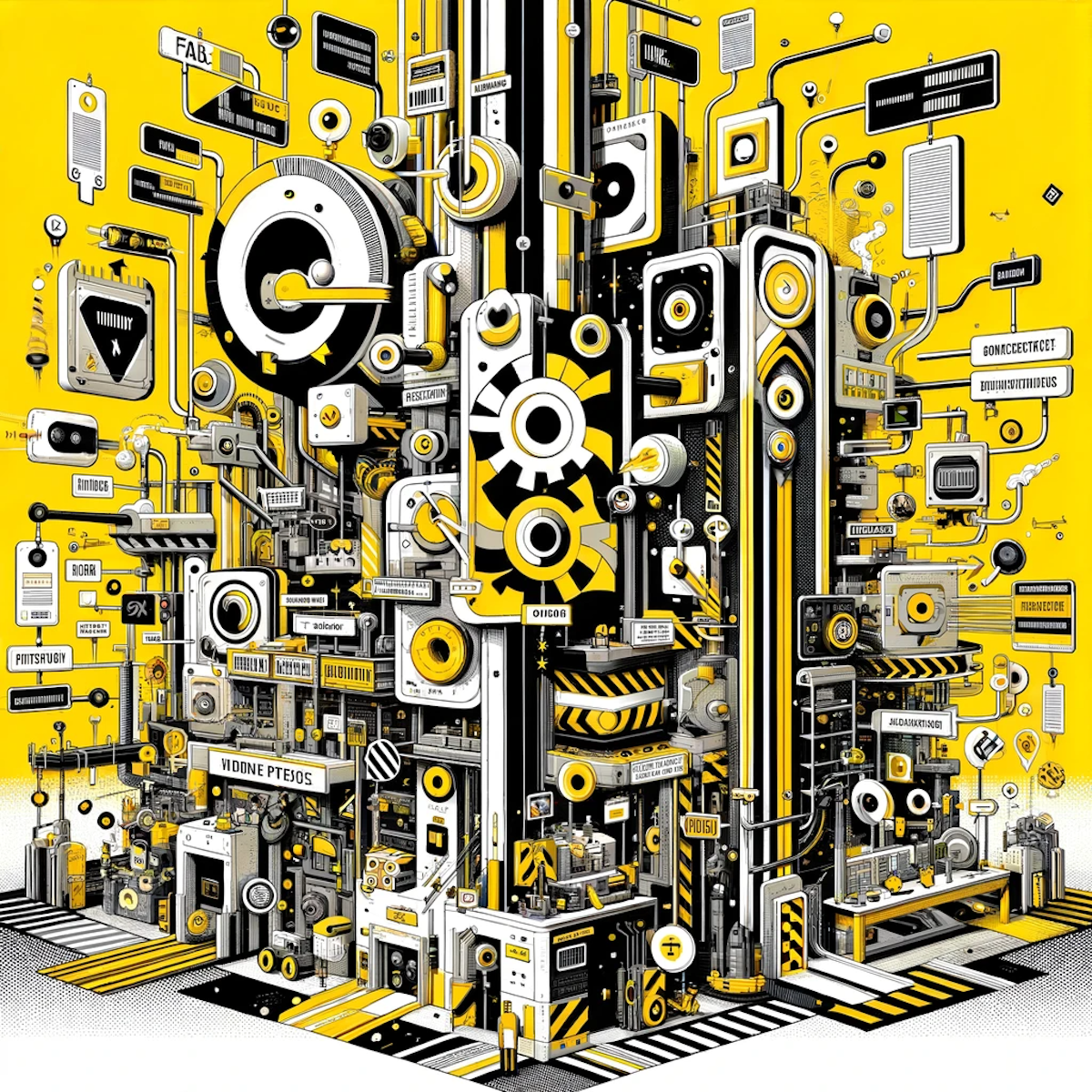
Background and definition of Poka-Yoke
Poka-Yoke, or error-proofing, finds its roots in the Japanese manufacturing sector, a testament to the country's relentless drive for Kaizen—continuous improvement. The term emerged from the Toyota Production System, an avant-garde that metamorphosed the automotive industry with its innovative approach to minimizing waste and optimizing efficiency. At the heart of Poka-Yoke is a philosophy that human error should not translate into defects; rather, mistakes should be engineered out of processes through intuitive design and the implementation of fail-safes.
Understanding Poka-Yoke as an error proofing technique
Poka-Yoke techniques manifest in various forms, ranging from simple physical fixtures that prevent incorrect assembly to sophisticated electronic detectors that halt a process when abnormal parameters are detected. The overarching aim is to either alert the operator to an impending error or to prevent the error's occurrence completely. Poka-Yoke approaches are not merely Band-Aids but ingrained components of systems that serve to ensure that operations are carried out without room for error.
Brief glimpse of the significance of Poka-Yoke in industries
The efficacy of Poka-Yoke spreads its tentacles across sectors, benefitting not just manufacturing but healthcare, service industries, and any domain where quality and reliability are paramount. By mitigating the impact of human errors, companies can save on costs associated with rework and scrap, enhance product quality, and, most importantly, imbue their customers with unwavering confidence in the brand’s commitment to excellence.
The Concept and Importance of Poka-Yoke
Deep diving into the concept of Poka-Yoke, its origin, and principles
To truly grasp the essence of Poka-Yoke, one must understand its central maxim: errors are natural, but they do not have to culminate in faults. The proactive nature of Poka-Yoke lies in its preliminary intervention—preventing lapses before they manifest as defects. The origin of Poka-Yoke, linked to the innovative visions of engineer Shigeo Shingo, reflects a profound understanding of the human aspect in manufacturing processes, where attention to detail can falter under the monotonous grind of repeated tasks.
Examination of why Poka-Yoke is crucial in process improvement
Within the pursuit of process improvement, Poka-Yoke emerges as a cornerstone, functioning seamlessly within the frameworks of Lean manufacturing and Six Sigma. Its role as a preventive measure—rather than a detective or corrective one—aligns perfectly with the objective of maximizing value through the elimination of waste, particularly the waste that arises due to errors and their aftermath.
Discussion on how Poka-Yoke aids in eliminating mistakes in a production process
Poka-Yoke aids the production process by methodically identifying potential error points and applying tailored solutions to forestall them. From jigs that ensure parts are presented in the correct orientation to sensors that verify the presence of components before a machine cycle starts, the employment of these innovations translates to a significant reduction in production hiccups.
Case Study Illustrating the Importance of Poka-Yoke
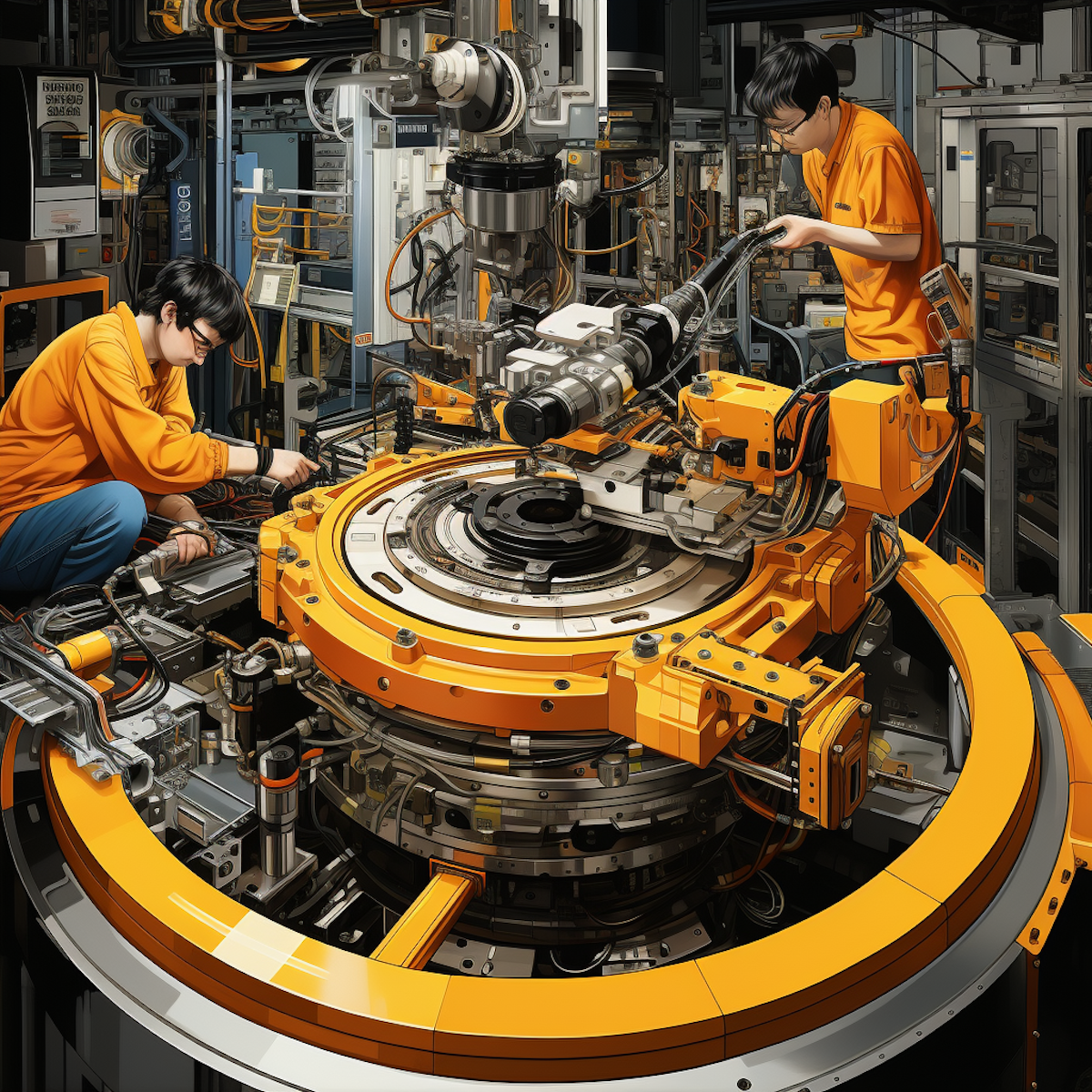
Poka-Yoke, a Japanese term that roughly translates to "mistake-proofing," is a key concept in lean manufacturing and quality management. It's used to design processes or mechanisms that prevent errors or make them immediately evident. The concept of Poka-Yoke can be categorized into two main types: Control and Shutdown. Here's a case study for each type to illustrate their importance:
Control Type Poka-Yoke: Automotive Manufacturing
Scenario: In an automotive assembly line, a Control type Poka-Yoke is implemented to ensure all parts are correctly installed.
Solution: A sensor-based system is set up at each assembly station. For example, when installing a car door, sensors detect if all required screws are in place. If a screw is missing, the system alerts the worker with a light signal and a sound. This immediate feedback prevents the car from moving to the next station with a missing or improperly installed part.
Outcome: This reduces the risk of defective cars reaching the final stages of assembly or, worse, the customer. It saves time and resources in detecting and rectifying errors, improving overall quality and customer satisfaction.
Shutdown Type Poka-Yoke: Chemical Manufacturing
Scenario: In a chemical manufacturing plant, there's a risk of overheating in reaction vessels, which can lead to dangerous situations.
Solution: A Shutdown type Poka-Yoke is implemented in the form of temperature sensors linked to an automatic shutdown mechanism. If the temperature in a reaction vessel exceeds a safe threshold, the system automatically shuts down the heating element and initiates a cooling process.
Outcome: This immediate and automatic response prevents potential accidents, ensuring the safety of workers and the facility. It also helps in maintaining product quality by avoiding reactions that run out of specified temperature ranges.
In both cases, Poka-Yoke mechanisms serve to enhance safety, quality, and efficiency. Control type Poka-Yokes ensure processes are completed correctly before moving forward, while Shutdown type Poka-Yokes take immediate action to prevent hazardous situations. These examples underscore the importance of integrating mistake-proofing techniques into various industries to foster a culture of safety and excellence.
Types of Poka-Yoke
Detailed discussion on the different types of Poka-Yoke with suitable examples
Poka-Yoke mechanisms can be broadly categorized into two types: control Poka-Yoke and warning (or shutdown) Poka-Yoke. Control Poka-Yokes are those that physically prevent an error from occurring, such as a template that only allows parts to be fitted in the correct way. On the other hand, shutdown Poka-Yokes halt the process if an abnormality is detected, compelling a correction of the error before resumption. This ensures that the part or product cannot proceed down the value stream until it meets the specified quality standard.
Analysis of the use-cases and effectiveness of Control and Shutdown type Poka-Yoke
The use-cases for these types of Poka-Yoke are extensive and varied. From electronic parts that cannot be inserted backward due to asymmetrical designs to software forms that validate input before submission, both methods ensure that error potential is squelched. Consideration of the dynamics of the respective process and environment dictates which Poka-Yoke type is most appropriate, with the ultimate goal of such systems being to render defects virtually impossible.
Examples of Control and Shutdown Poka-Yoke
To provide a more detailed understanding of Poka-Yoke in action, let's delve into two specific case studies, one each for Control and Shutdown Poka-Yoke.
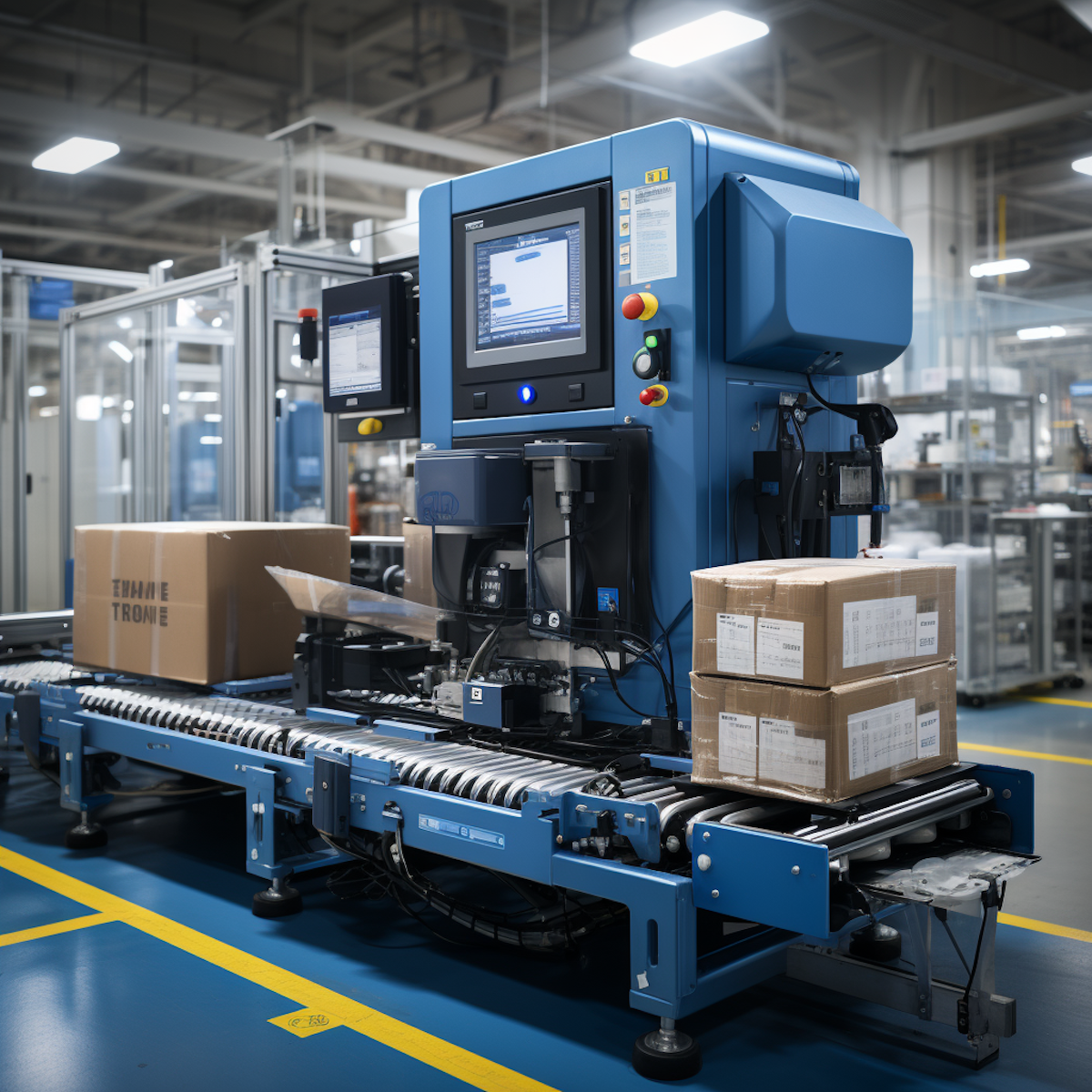
Control Poka-Yoke: Medical Device Packaging
Background
A medical device company faced challenges in ensuring the correct number of items were packaged. Missing or extra items in the package could lead to serious health risks for patients and legal issues for the company.
Implementation
The company implemented a Control Poka-Yoke system in their packaging line. This system included:
Weight Check: Each package was weighed after assembly. The weight data was cross-referenced with the expected weight for the correct number of items.
Visual Confirmation System: High-resolution cameras were installed to take images of each package’s content. Image recognition software then verified the presence and correct placement of each item.
Error Notification: If a discrepancy was detected, the system immediately alerted the operator with an audible alarm and a visual cue on a control monitor.
Outcome
This system significantly reduced packaging errors. The company reported a 99% reduction in customer complaints related to packaging errors and a noticeable improvement in operational efficiency, as fewer resources were needed for quality control and error rectification.
Shutdown Poka-Yoke: Automotive Manufacturing
Background
An automotive manufacturing plant faced issues with its painting booth. Occasionally, the painting robots would malfunction, leading to overpainting or uneven paint layers, which required costly rework.
Implementation
A Shutdown Poka-Yoke system was introduced:
Real-time Monitoring: Sensors were placed to monitor the paint flow rate, nozzle pressure, and robot arm speed.
Automatic Shutdown: If any parameter went beyond the predefined range, the system would automatically shut down the painting process.
Immediate Alert: Along with the shutdown, the system sent an immediate alert to the control room for quick intervention and diagnosis of the issue.
Outcome
This proactive approach reduced the frequency of painting errors. The automatic shutdown prevented the waste of paint and reduced the time spent on reworking defective units. The plant reported an improvement in paint quality and a reduction in material wastage.
In both these cases, Poka-Yoke systems provided effective solutions to specific problems. The Control Poka-Yoke in medical device packaging ensured accuracy and safety, while the Shutdown Poka-Yoke in automotive manufacturing enhanced quality and efficiency. These examples highlight the versatility and impact of Poka-Yoke in different industries, proving its value in error prevention and quality assurance.
Implementing Poka-Yoke in Business Processes
Essential steps and strategies to effectively implement Poka-Yoke in various business processes
Implementing Poka-Yoke is an exercise in meticulous observation and innovative problem-solving. The first step is to identify the stage at which errors arise within a process and understand the root causes. Once identification is complete, businesses can brainstorm and test various Poka-Yoke mechanisms that could corral these errors. Strategically, this may involve simple physical modifications, systemic adjustments, or comprehensive redesigns of a process.
Discussion on the stages of implementation, from identification of a problem to integrating a Poka-Yoke solution
The stages of Poka-Yoke implementation typically involve initial problem identification, conceptual design of potential solutions, pilot testing and refinement, and final integration of the chosen Poka-Yoke into the process. Rigorous testing and iterative improvement are crucial at each stage to ascertain the Poka-Yoke’s effectiveness and its integration into the workflow without causing additional complications.
Importance of employee training and change management during Poka-Yoke implementation
For Poka-Yoke solutions to be embraced and effective, the workforce must be educated on their use and benefits. Training programs and inclusion of team members in solution design can foster a culture of proactive error prevention. Additionally, change management is crucial to address resistance and ensure a smooth transition to new or modified processes.
Case Study Illustrating Poka-Yoke Implementation
The service sector often benefits greatly from Poka-Yoke as it helps in reducing errors in customer service, billing, and other operational processes.
Case Study: Poka-Yoke in a Banking Institution
Background
A prominent banking institution was facing challenges with its online banking services. Customers frequently made errors while conducting transactions, such as transferring funds to the wrong account or entering incorrect amounts, leading to customer dissatisfaction and a high volume of error correction requests.
Poka-Yoke Implementation
Confirmation Steps: The bank introduced additional confirmation steps in the online transaction process. After a customer entered transaction details but before finalizing the transaction, a detailed summary of the transaction was displayed, asking the customer to confirm the accuracy of the details.
Limit Checks: The bank implemented limit checks for transactions. Customers were required to set up daily transaction limits. If a transaction exceeded this limit, it would trigger a secondary authorization process, such as a phone call or a secure email.
Template Transactions: For regular transactions, customers were encouraged to set up templates with pre-filled information for recipients they frequently transacted with. This reduced the likelihood of entering incorrect details for each transaction.
User-Friendly Error Messages: The online banking platform was enhanced to provide clear, user-friendly error messages and guidance in case of incorrect data entry, helping customers correct errors on the spot.
Outcomes
Reduction in Transaction Errors: There was a significant decrease in the number of incorrect transactions, as customers were more likely to catch and correct errors due to the confirmation steps and clear error messages.
Improved Customer Satisfaction: Customers expressed greater satisfaction with the online banking experience as the process became more secure and user-friendly.
Operational Efficiency: The bank experienced a reduction in the workload of its customer service department, as fewer customers needed assistance with correcting transaction errors.
This case study demonstrates how Poka-Yoke, traditionally associated with manufacturing, can be effectively applied in the service industry. By introducing simple, thoughtful changes in the online banking process, the bank was able to significantly reduce customer errors and enhance the overall service experience. This highlights the versatility of Poka-Yoke as a tool for improving quality and efficiency across various sectors.
Beyond Manufacturing – Poka-Yoke in Service Industries
Exploration of how Poka-Yoke can be applied outside the manufacturing sector
Poka-Yoke transcends the borders of manufacturing and has found fruitful soil in the service sector as well. Financial institutions use form auto-fill features to reduce data entry errors, while healthcare providers employ standardized checklists to ensure all procedural steps are followed correctly. Even the IT industry embraces Poka-Yoke through automated code reviews and error checking before deployment.
Brief explanation of Poka-Yoke use in service industries such as healthcare, finance, and IT
In healthcare, Poka-Yoke can translate to fewer medical errors and improved patient outcomes. The financial industry uses Poka-Yoke to ensure compliance with regulations, while in IT, it facilitates the smooth operation of systems and security protocols. Across the service spectrum, Poka-Yoke serves as a safeguard against lapses, be they logistical, technical, or human.
Examination of the benefits and impact of Poka-Yoke in these industries
The impact of Poka-Yoke in service industries is not just in the quality of the output but in the experience of both the provider and the customer. Avoiding errors enhances customer satisfaction, bolsters the business reputation, and contributes to a cycle of continuous improvement. It is both a protective measure and a strategic advantage.
Case Study Illustrating Poka-Yoke in Service Industry
To provide a detailed analysis of the practical application and benefits of Poka-Yoke in the service industry, let's examine a case study from the hospitality sector, specifically a hotel chain.
Case Study: Poka-Yoke Implementation in a Hotel Chain
Background
A multinational hotel chain was experiencing issues with guest check-ins and room assignments. Mistakes in assigning rooms that were already occupied or not properly cleaned led to guest dissatisfaction and operational inefficiencies.
Poka-Yoke Implementation
Room Status Tracking System: The hotel introduced an electronic room status tracking system. This system was integrated with the housekeeping department, allowing real-time updates on room status – whether it was clean, occupied, or needed maintenance.
Automated Check-In Process: The hotel implemented an automated check-in process through a mobile app. Guests could check-in via the app, which was programmed to only assign rooms that were marked as 'clean and ready' in the room status tracking system.
Double-Verification for Room Assignment: At the front desk, employees were required to perform a double-verification step before issuing room keys. The system automatically cross-checked the room status and alerted the staff if the selected room was not ready.
Feedback Loop with Guests: After room assignment, guests received an automated message asking them to confirm the condition and acceptability of the room. Any negative response triggered an immediate alert to the front desk and housekeeping.
Outcomes
Reduction in Room Assignment Errors: The hotel saw a significant decrease in the number of incidents where guests were assigned to incorrect or unready rooms.
Enhanced Guest Satisfaction: The streamlined check-in process and the assurance of getting a ready room improved the overall guest experience, as reflected in higher satisfaction ratings and positive reviews.
Increased Operational Efficiency: The real-time room status updates and automated processes reduced the workload and error rate for front desk and housekeeping staff, leading to more efficient operations.
This case study illustrates how Poka-Yoke principles, traditionally associated with manufacturing, can be effectively applied in the service industry to enhance customer satisfaction and operational efficiency. The hotel chain's implementation of a room status tracking system, an automated check-in process, double-verification for room assignments, and a guest feedback loop are prime examples of Poka-Yoke techniques that prevent errors and ensure service quality. This approach not only improved the guest experience but also streamlined internal processes, showcasing the broad applicability and benefits of Poka-Yoke in service-oriented settings.
Conclusion – The Power of Poka-Yoke
Restatement of the core ideas discussed in the blog
Poka-Yoke stands as a testament to the ingenuity inherent in the pursuit of flawless execution, imbuing processes with the resilience needed to withstand the fallibility of human nature. From its origins in the Japanese manufacturing sphere to its proliferation across sectors, Poka-Yoke embodies a universal principle: error prevention is the keystone of quality.
Emphasis on the importance of Poka-Yoke for business process improvement
For any entity vested in the relentless quest for excellence and efficiency, the integration of Poka-Yoke stands not just as a tactic, but a strategic imperative. With its dual capacity to improve quality and reduce costs, Poka-Yoke is a pivotal component in business process improvement landscapes.
Encouragement for the adoption of Poka-Yoke for error reduction in various sectors
Businesses that embrace Poka-Yoke, be it through an online certificate course or a heavyweight problem-solving certification, position themselves at the forefront of a competitive marketplace that prizes quality, reliability, and innovation. Evoking the wisdom and foresight of its pioneers, businesses can wield Poka-Yoke as both shield and sword in the battle for business supremacy.